In processing PVC wood plastic foam board, the equipment can be divided into the single-layer skin foam board production line and the three-layer coextrusion foam board production line according to the processing and board types. According to the production process, it is divided into the twin-screw extrusion and the single screw extrusion.
(1) Single-layer skin foam board production line and three-layer coextrusion foam board production line
The single-layer skin foam plate production line adopts one main extruder to directly squeeze into the die for extrusion foaming molding, which has simple production process control and convenient equipment disassembly and cleaning.
The three-layer coextrusion foam plate production line adopts two extruders, one is the main extruder, and the other is the auxiliary extruder. The two extruders are placed at a certain angle. The auxiliary extruder extrudes the melt, which is evenly distributed to the upper and lower layers of the melt of the main extruder through the die distributor. The two non-foaming hard surfaces are obtained through die extrusion and cover the surface of the high foaming core composite plate products. It features large surface hardness, high core filling, high foaming, and low cost. But at the same time, its disadvantages are distinct. The production process is complex, the control requirements of the compound layer process formula are accurate, and the equipment disassembly and cleaning are difficult.
(2) Single screw extruder and twin screw extruder
The production process determines whether a single-screw extruder or twin-screw extruder is used in production. The single-screw extruder has one more granulation process than the twin-screw extruder in terms of product quality. The melt plasticization uniformity and the mixing of various additives are more uniform, and the product quality is better than the one-step twin-screw direct powder extrusion. In terms of the production process, the single-screw extruder has more granulation steps, which means that one more extruder increases energy consumption, workforce, and material resources, and the production cost is much higher than that of a twin-screw extruder. In terms of production speed, the twin-screw process has few steps and fast extrusion speed, and the efficiency is much higher than that of the single screw process. With the continuous improvement of the wood-plastic formula and the constant optimization of the twin-screw structure, the plate quality produced by the twin-screw has reached the level of single screw production.
Due to the characteristics of low energy consumption and high efficiency of twin-screw extruder, twin-screw extruder has completely replaced single screw extruder in the production of PVC wood plastic foam board.
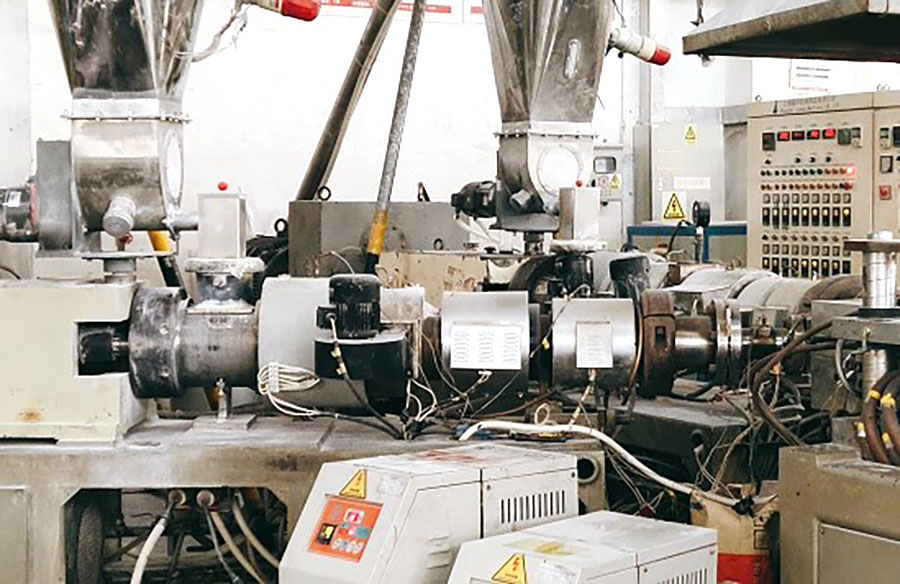
Leave a Reply
Want to join the discussion?Feel free to contribute!